Laws on random drug testing in the workplace
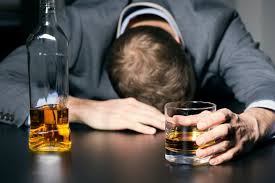
Drug testing can be quite a difficult and time-consuming policy to establish. Remember, an organisation must have consent from its employees to test them for drugs. This consent is usually included in the individual’s contract.
The law imposes various requirements on employers who wish to undertake random drug testing in the workplace. These include:
• limiting drug testing to the specific group of employees that the organisation needs to test
• ensuring the tests are random
• not singling out an employee unless justified by the nature of their job.
If there is a policy, with procedures in place and an employer has good reasons for testing for drugs — whether it is essential to do so for certain roles or where there is reasonable cause to believe an employee is under the influence — and someone refuses to take the test, the employer may resort to disciplinary action.
Dealing with drugs in the workplace
So, once an organisation has established when testing is applicable, how does it go about the testing?
There are three different types of workplace drug and alcohol testing.
- Pre-employment: This tends to be the most common form but it’s also the least effective. This is because it’s based on a urine sample that an individual can easily dilute or substitute.
- Post-incident: As the name suggests, testing in this case follows a health and safety incident.
- Random: When a group of individuals consent to testing and you pick a handful of them to test at random.
To effectively test for drugs, the testing must be carried out by an individual with the correct qualifications from the UK Accreditation Service. They’ll conduct the testing.
The testing procedure must also comply with the International Standard for Laboratories. Failing to do this will mean the results are void.
Drug tests tend to work in a similar way, no matter which substance you are testing for. The most common package test is for cannabis, cocaine, amphetamine, methamphetamine, benzodiazepine, and opiates.
What to do if drugs are found in the workplace
If you happen to find physical evidence of employees using or storing drugs in the workplace, you still have to follow your process.
- Refer back to your drug and alcohol policy and stick to it.
- Document where, how, why, and who found the drugs, as well as any witnesses, previous complaints, concerns or behaviours.
- Meet with the employee to discuss the situation — you should bring your documents with you to support this. Make sure a third party is present as a witness.
- If the discussion with the employee is inconclusive, you may request the employee submits to a drug test.
- If the employee refuses to take a test you may go down the disciplinary route — including terminating their employment if necessary.
The organisation should consider to what degree, if an employee is found to be using drugs, it will offer help and support. Actions might include arranging sick leave for treatment and arranging for referral to a treatment service.
How to create a drug and alcohol policy
The aim of this policy is to clearly set out the company’s position on drugs and alcohol within the workplace. You should include this in your Health and Safety Policy.
- The policy should define when the use of drugs or alcohol is an issue (For example within working hours or when it interferes with work capability or conduct, etc). Make sure that you have considered the effects of prescription drugs too.
- Then, it should define when the organisation might request a drug test or conduct an investigation.
- It should then give direction to employees who suspect a colleague is under the influence, ideally pointing them to a particular contact they can speak to.
- Finally, the policy should detail the company’s support and disciplinary procedures and how it will relate to anyone using drugs or alcohol in the workplace.
You may also want to create a separate document that specifically covers drug testing. The document needs to be specific to your organisation and work activities.
Contact us should you wish to discuss this topic or create a policy.