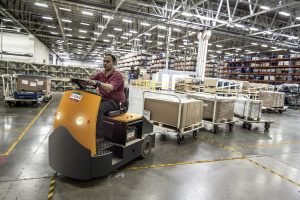
Warehouse health and safety tips
Warehouse health and safety tips
Health and safety procedures are paramount in any workplace, but warehousing roles present specific risks that all workers should be aware of. First, it’s important to note that we understand how easy it can be to to let initial training fall to the wayside as you grow in confidence and find yourself in an everyday routine – this is normal in many jobs.
However, letting your guard down in a high-risk environment can not only put you in danger, but it can also expose your colleagues to the risks of the work place too. So, it certainly pays to be educated when it comes to warehouse health and safety.
Whether you are an employer or an employee, there are certain requirements that must be met within the warehousing industry. Below are some of the main legal requirements for employers in the UK warehousing industry:
It is imperative that all aspects of health and safety training are covered by management. These include training in:
Why is training so important for warehousing staff?
Warehousing logistics are complex, and typically this type of work environment never sleeps. For this reason alone, it can be a manic environment to be in, especially if you’re not up to date with recent training strategies.
There are a huge range of benefits to training warehousing staff, not least to improve efficiency, increase staff morale and offer job fulfilment, but also to equip staff with everything they need to stay safe at work.
As we have stated, warehouses pose a plethora of risks, from moving vehicles to high objects, there is the potential for all kinds of incidents to occur, and so it is vital that every person on the premises is equipped with the skills and knowledge to safely handle any workplace eventuality.
Due to the size and layout of most warehouses, the need for up to date and accurate fire safety training is absolutely paramount. Regular fire safety assessments and subsequent training is actually a workplace requirement regardless of the industry you’re in, but in the case of warehouses which have a number of hazards, it’s even more important that this is kept on top of.
Things that must be carried out by employers, supervisors or management include:
Some important fire safety measures which should be carried out in the workplace include:
Effective and appropriate personal protective equipment (PPE) is often required as part of a larger health and safety strategy within a warehouse environment. It is important to ensure that you are wearing the appropriate attire to carry out your role, however this must be in conjunction with other measures in the case of your PPE failing.
It is a legal requirement here in the UK to supply all workers with appropriate PPE, and in a warehouse environment these can include:
Along with appropriate training in the appropriate PPE, regular risk assessments must also be carried out in the warehouse to ensure the right PPE is in place. Where new risks occur, old measures may need to be removes, and different PPE may need to be put into place.
In most warehouses in-house vehicles are an essential aspect of every day. Used typically for the safe moving and handling of goods, workers operating such vehicles are required to hold specific licenses.
Training is essential not just for those handling warehouse vehicles, but also for others who may come into contact with vehicles during their working day. Thorough training on how to use vehicles, and knowledge of best practice can help to maintain a safe environment. Here are some things to consider:
In any work environment there’s likely to be a risk of slips and trips, whether that’s in the kitchen or out on the shop floor. In a warehouse it can occur more easily due to things such as the surface of the floor, cables from vehicles or spills.
Here are some things you can do to avoid accidents from happening:
A huge part of your work in a warehouse will likely involve moving and handling large, often heavy goods. Doing so without the proper training however can lead to severe injuries, some of which can even put you out of work.
Luckily, there are simple things you can do to prevent injury from moving and handling goods, these include:
Incorrect handling can lead to a wealth of physical conditions, including the following:
As well as the way you hold yourself and handle goods in transit, the way you pack them can also make a huge difference to your physical wellbeing. Below are some of our tips for the safe packing of goods:
Health and safety aren’t as straightforward as we might like, especially in high-risk environments such as warehouses. But it’s crucial that we stay educated and up to date with both theoretical and practical training in order to stay safe at work.
If you are unsure about any aspects of today’s guide, it may be worthwhile to have a conversation with your manager about training opportunities. After all, it pays to be prepared.
Contact us for further information.