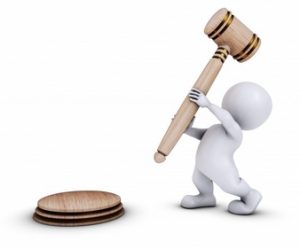
What is RIDDOR?
Why have this talk? Exposure to vibration can result in serious injury and disability.
Also, vibration and sound waves can travel through the ground and cause disturbances to the environment and local community, as well as causing structure damage over time.
What will this talk cover? The sources, effects, and methods of overcoming excessive vibration and reducing nuisance to others from vibration.
Who is most at risk? Those who regularly use high-vibration tools, equipment and machines.
Harm caused by vibration
Hand–arm vibration damage is mostly caused by hand-held power tools, for example
Whole-body vibration can be caused by, for example:
Do you have any questions for me?
Contact us for further information.
What is a fire risk assessment?
A fire risk assessment helps you to identify risks from fire hazards on your premises and work out what actions you need to take to make sure any risk is as low as reasonably possible.
Help with the fire risk assessment?
A responsible person must carry out and regularly review a fire risk assessment of the premises. This will identify what you need to do to prevent fire and keep people safe.
You can do the fire risk assessment yourself with the help of standard fire safety risk assessment guides. Alternatively, if you do not have the expertise or time to do the fire risk assessment yourself you need to appoint a ‘competent person’ to help, contact us for further details.
You’ll need to consider:
We have put together an infographic. I would recommend that you share the information with employees as it could be beneficial to them.
Contact us for further information.
Why have this talk? More than one third of accidents that killed workers in 2019–20 were from falls from height. 50% of all falls over 2 metres result in death.
What will this talk cover? The hazards faced and how to prepare if you are working at height.
Working at Height Toolbox Talk
What is working at height?
Any work situation where you could fall and injure yourself and others. So it includes working above or below ground level on platforms, trap hatches, on top of vehicles as well as ladders and roofs.
Hazards to consider when working at height
Before working at height
Safe working on roofs
Questions for employees
Contact us for further information
What is RIDDOR?
There are certain rules and regulations regarding RIDDOR, these include keeping all records up to date, having an accident book so accidents that don’t need to be reported to RIDDOR can be recorded.
There are certain rules and regulations regarding RIDDOR, these include keeping all records up to date, having an accident book so accidents that don’t need to be reported to RIDDOR can be recorded.
It is advised that RIDDOR records are kept for 5-6 years however the minimum they must be kept for is 3 years.
In October 2013, new RIDDOR regulations came into place, there were some changes, the list of ‘major injuries’ in RIDDOR 1995 was replaced with ‘Specified injuries’ in 2013.
The 1995 schedule that detailed 47 different types of industrial disease was replaced with eight categories of reportable work-related illness.
There was also a change in the types of dangerous occurrences that needed to be reported, in 2013 there were less.
In many different workplaces RIDDOR applies, In 2013 RIDDOR was revised, now it requires a responsible person to report to the enforcement agency, as well as keeping records.
A responsible person is –
The responsible person only needs to report to the HSE when a accident or incident has occurred in relation to work. So, if something happens to a worker when they are on their way home from work. It doesn’t need to be reported under RIDDOR.
RIDDOR reportable, deaths and injuries must have occurred – As a result of an accident to workers, self-employed and non-workers that has caused injury to them.
Or from a work-related accident that arise out of or in connection with work, the work itself must have contributed to the accident, as well as whether any plant, substance or equipment were involved. The condition of the workplace can also have an impact on whether an accident is reportable.
It is important to report any accidents and incidents as they are warnings that there are uncontrolled hazards that need identifying and eliminating to help prevent any more accidents in the future, or worse a serious accident that could cost someone their life.
There are certain things that don’t have to be reported under RIDDOR 2013, it is important to know what these are so that you don’t end up not making a RIDDOR report when you should have done.
Contact us for further information.
Warehouse health and safety tips
Health and safety procedures are paramount in any workplace, but warehousing roles present specific risks that all workers should be aware of. First, it’s important to note that we understand how easy it can be to to let initial training fall to the wayside as you grow in confidence and find yourself in an everyday routine – this is normal in many jobs.
However, letting your guard down in a high-risk environment can not only put you in danger, but it can also expose your colleagues to the risks of the work place too. So, it certainly pays to be educated when it comes to warehouse health and safety.
Whether you are an employer or an employee, there are certain requirements that must be met within the warehousing industry. Below are some of the main legal requirements for employers in the UK warehousing industry:
It is imperative that all aspects of health and safety training are covered by management. These include training in:
Why is training so important for warehousing staff?
Warehousing logistics are complex, and typically this type of work environment never sleeps. For this reason alone, it can be a manic environment to be in, especially if you’re not up to date with recent training strategies.
There are a huge range of benefits to training warehousing staff, not least to improve efficiency, increase staff morale and offer job fulfilment, but also to equip staff with everything they need to stay safe at work.
As we have stated, warehouses pose a plethora of risks, from moving vehicles to high objects, there is the potential for all kinds of incidents to occur, and so it is vital that every person on the premises is equipped with the skills and knowledge to safely handle any workplace eventuality.
Due to the size and layout of most warehouses, the need for up to date and accurate fire safety training is absolutely paramount. Regular fire safety assessments and subsequent training is actually a workplace requirement regardless of the industry you’re in, but in the case of warehouses which have a number of hazards, it’s even more important that this is kept on top of.
Things that must be carried out by employers, supervisors or management include:
Some important fire safety measures which should be carried out in the workplace include:
Effective and appropriate personal protective equipment (PPE) is often required as part of a larger health and safety strategy within a warehouse environment. It is important to ensure that you are wearing the appropriate attire to carry out your role, however this must be in conjunction with other measures in the case of your PPE failing.
It is a legal requirement here in the UK to supply all workers with appropriate PPE, and in a warehouse environment these can include:
Along with appropriate training in the appropriate PPE, regular risk assessments must also be carried out in the warehouse to ensure the right PPE is in place. Where new risks occur, old measures may need to be removes, and different PPE may need to be put into place.
In most warehouses in-house vehicles are an essential aspect of every day. Used typically for the safe moving and handling of goods, workers operating such vehicles are required to hold specific licenses.
Training is essential not just for those handling warehouse vehicles, but also for others who may come into contact with vehicles during their working day. Thorough training on how to use vehicles, and knowledge of best practice can help to maintain a safe environment. Here are some things to consider:
In any work environment there’s likely to be a risk of slips and trips, whether that’s in the kitchen or out on the shop floor. In a warehouse it can occur more easily due to things such as the surface of the floor, cables from vehicles or spills.
Here are some things you can do to avoid accidents from happening:
A huge part of your work in a warehouse will likely involve moving and handling large, often heavy goods. Doing so without the proper training however can lead to severe injuries, some of which can even put you out of work.
Luckily, there are simple things you can do to prevent injury from moving and handling goods, these include:
Incorrect handling can lead to a wealth of physical conditions, including the following:
As well as the way you hold yourself and handle goods in transit, the way you pack them can also make a huge difference to your physical wellbeing. Below are some of our tips for the safe packing of goods:
Health and safety aren’t as straightforward as we might like, especially in high-risk environments such as warehouses. But it’s crucial that we stay educated and up to date with both theoretical and practical training in order to stay safe at work.
If you are unsure about any aspects of today’s guide, it may be worthwhile to have a conversation with your manager about training opportunities. After all, it pays to be prepared.
Contact us for further information.