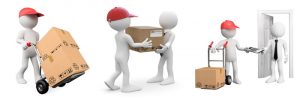
Health and Safety Hazards
According to statistics provided by the Health and Safety Executive (HSE), in the UK in 2020/2021:
Menopause awareness is about celebrating women as they age! Since 2009, the International Menopause Society (IMS), in collaboration with the World Health Organization (WHO), has designated October as World Menopause Awareness Month, with October 18 celebrated as World Menopause Awareness Day.
On our infographic, we look at the symptoms, help, and support that people are able to receive.
Did you know temporary cognitive impairment affects over 40%* women at some point during their menopause transition? Here are some tips to keep the cogs working!
Tip 1: Keep Hydrated.
Tip 2: Take a break outside.
Tip 3: Shower with your eyes closed.
Tip 4: Anchoring.
Tip 5: Invest in some noise-cancelling headphones.
If you would like to find out more click on the links below:
Reach out for advice Menopause Matters, menopausal symptoms, remedies, advice
Read one of our past blogs https://www.walkersafety.co.uk/blog/2020/09/menopause-at-work-risk-assessments-policies-guidelines/
Click on our wellbeing page for further information. Wellbeing | Walker Health and Safety Services (walkersafety.co.uk)
Contact us if you require further information.
Health and safety audits and inspections are beneficial to a company.
Reasons why you should conduct a health and safety audit:
Take a read through out infographic. Contact us if you would like to discuss your companies health and safety management system, risk assessments or audits and inspections.
The relevant legislation is the Health and Safety (First-Aid) Regulations 1981, which requires employers to provide adequate and appropriate equipment, facilities and personnel to ensure their employees receive immediate attention if they are injured or taken ill at work. However, as what is ‘adequate and appropriate’ will depend on the circumstances in the workplace, the findings of the employer’s first aid needs assessment should help them determine what they would need to provide. So, if the employer’s original assessment identified first aiders are necessary due to the hazards/risks associated with the work etc, this wouldn’t change as the nature of the work is the same, just with fewer people.
Regulation 3 states the duty of an employer to make provision for first aid and the accompanying guidance covers needs assessment, work patterns, how many first aiders are needed and appointed persons.
The Health and Safety Executive’s (HSE’s) first-aid section states: “In the event of injury or sudden illness, failure to provide first aid could result in a casualty’s death. The employer should ensure that an employee who is injured or taken ill at work receives immediate attention.
“HSE will prosecute in cases where there is a significant risk, a disregard for established standards or persistent poor compliance with the law.”
There are plenty of pre-made first aid kits available and many stockists offer kits tailored to specific situations such kits for outdoor activities and ones for in the office.
Use this toolbox talk to provide employees with information for first aid.
Contact us for further information.
Health and Safety Hazards
According to statistics provided by the Health and Safety Executive (HSE), in the UK in 2020/2021:
What is a health and safety hazard?
A hazard is something that has the potential to cause harm or damage or have an adverse effect on a person or people. Many people confuse the words hazard and risk, especially in relation to occupational health and safety. The risk or level of risk is the likelihood that a person may be harmed or experience an adverse effect if they are exposed to a hazard. In other words, it is the likelihood that a hazard will have a negative impact on an individual’s health and safety.
Health and safety hazards can come from a variety of sources. Hazards can be substances, materials, processes and practices that can cause harm.
The most common health and safety hazards are:
Biological hazards
Biological hazards, often referred to as biohazards, can be any biological or organic substances that have the potential to cause harm or pose a threat to a person’s health. You may be exposed to biological hazards if you work with animals, people or infected plants. Biological hazards can have adverse health effects and in extreme circumstances can result in death.
Biological hazards can be found in a variety of workplaces, including hospitals, laboratories, schools, care homes, farms, and within the food industry.
An individual can be exposed to a biological hazard by having contact with any of the following:
Biological hazards are classified into four groups, depending on the level of risk of infection to humans, with Group 1 having the lowest risk and Group 4 having the highest risk.
Biological hazards can be transmitted in several ways, including by injection, absorption, ingestion or inhalation.
Chemical hazards
Chemical hazards are hazardous chemicals that can be in the form of a solid, liquid or gas. Some chemicals are more hazardous than others and they can result in a huge variety of health and physical effects, including skin irritation, breathing problems, respiratory system irritation and blindness.
Chemical hazards can be found in a variety of everyday products, meaning that many homes and workplaces involve a risk of coming into contact with chemical hazards, including hair salons, florists, restaurants, bars, schools and cleaning companies.
Chemical hazards may be present in the following products:
Hazardous chemicals are categorised according to how dangerous they are. Some of the categories include Harmful, Toxic, Very Toxic, Corrosive, Flammable, Extremely Flammable, Oxidising Agent, and Explosive.
Physical hazards
Physical hazards cannot always be seen or touched. They can be any factor or condition of the environment that can harm a person, even if they do not touch them.
People in a variety of environments can be exposed to physical hazards, including construction, demolition and excavation, as well as those who spend long periods outside.
Some examples of physical hazards include:
Ergonomic hazards are a result of physical factors such as body positions, the type of work you are undertaking, and any working conditions that can put a strain on your body. Many ergonomic hazards occur over time and can result in musculoskeletal injuries. Ergonomic hazards are often related to manual handling and can be found in all types of workplaces.
Musculoskeletal injuries can have significant short-term and long-term impacts on a person’s health and wellbeing.
They affect the musculoskeletal system which includes the muscles, tendons, bones, joints, ligaments, nerves and blood vessels. Common musculoskeletal injuries include back injuries, upper limb or neck disorders, lower limb disorders, and damage to joints or other tissue.
Ergonomic hazards include:
Safety hazards are hazards that create unsafe working conditions. Unsafe working conditions can cause injury, illness or even death. Safety hazards can be found in homes and workplaces across the UK.
Safety hazards can cause a significant number of injuries or illnesses and can even result in death.
Some examples of safety hazards include:
Environmental hazards are substances, states or events that can cause harm to people or have an adverse effect on their health. They are usually related to the weather, temperature and climate. They may be unpredictable or frequently changing, which is one of the reasons why they are considered hazardous.
Some examples of environmental hazards include:
Also known as work organisational hazards, these are hazards that can affect an employee’s mental health and wellbeing. An employee can experience both short-term and long-term effects of psychosocial hazards.
Some examples of psychosocial hazards include:
In 2021, the Health and Safety Executive (HSE) reported that there were 74,000 work-related injuries and illnesses in the constructions industry alone. Nearly 40,000 of these injuries were musculoskeletal disorders. Individuals who work in the construction industry are 2-3 times more likely to experience a workplace injury compared to other industries.
The main reason for the higher incidence of injuries in the construction industry is the high number of health and safety hazards.
Some of the most common health and safety hazards in the construction industry are:
Under the Health and Safety at Work etc Act 1974, employers are required by law to conduct a risk assessment of health and safety hazards on construction sites. This can help to reduce the number of hazards you are exposed to on a construction site.
However, self-employed and employed construction workers are not required to conduct a risk assessment if less than five people are working for them. This could mean that hazards and risks are not always reduced to the lowest possible level.
If you become aware of any hazards on a construction site you are working on, it is important that your report these hazards to the relevant people. This could be your employer, supervisor, a health and safety manager, or the site manager.
If you believe these concerns have not been taken seriously, or the hazard has not been dealt with, you could contact the Human Resources department of your company.
Alternatively, you can contact the Health and Safety Executive (HSE) directly. HSE is responsible for enforcing health and safety in many industries and workplaces across the UK.
There are many different members of staff working in different capacities and departments within a hospital. This includes doctors, nurses, other healthcare professionals, cleaning staff and administrative staff.
Health and safety hazards in hospitals can also differ depending on the area of the hospital you work in and the role you fulfil. Health and safety hazards can also affect patients and visitors to the hospital.
Being aware of potential hazards and removing or reducing them to the lowest possible level is therefore essential.
Some of the most common health and safety hazards in hospitals include:
All hospitals in the UK should have current risk assessments for many of the tasks, activities and operations that take place. However, if you believe the risk assessment is not accurate, or you have identified other hazards or risks, there are several procedures you can follow.
If you are a member of hospital staff and you need to report a health and safety hazard, the first person you should speak to is your line manager. Alternatively, you can consult another manager within the hospital or speak to the Human Resources department.
Many hospitals and healthcare settings will also have a formal system in place where you can submit a written report of your concerns.
If the issue concerns patient safety, NHS staff and the general public are encouraged to report the issue on the National Reporting and Learning System (NRLS). This helps the NHS to identify hazards and risks and improve patient safety.
Health and safety hazards in offices
Many people in the UK work in an office. You may think that an office is less hazardous than other workplaces, and although you are statistically less likely to incur an injury in an office compared to on a construction site, health and safety hazards in the office still exist and should be taken seriously.
Some of the most common health and safety hazards in an office are:
If you need to report a health and safety issue or the presence of hazards in your office, you should speak to your line manager or the office manager. Alternatively, you can contact your office or company’s Human Resources department or your union representative.
If you feel that your office is not taking your concerns seriously, or that the issue you need to report is especially serious, you can contact the Health and Safety Executive (HSE) and make a report on their website or via phone.
Health and safety hazards in warehouses
Ensuring the health and safety of warehouse staff can be difficult due to the many different tasks, activities and operations that are performed in a warehouse.
This can include handling heavy loads, operating machinery and equipment, packaging goods, assembly, production, loading and unloading goods, preparation of orders, and shipping.
Many health and safety hazards can be found in warehouses and if these hazards are not eliminated or reduced to the lowest possible level, employers are risking the health and safety of their employees.
Some of the most common warehouse health and safety hazards are:
Any warehouse employee who becomes aware of a hazard should report it as soon as possible. Your warehouse should have a procedure for reporting hazards and other health and safety concerns, and you should follow this procedure to ensure that the appropriate manager or supervisor can deal with the hazard as quickly as possible.
Health and safety hazards in food manufacturing
Food safety hazards can cause foodborne illnesses, injuries and allergic reactions. Hazards can affect food throughout the entire food processing, including during manufacturing.
As well as the health and safety hazards that can cause illness or injury to consumers, hazards within the food manufacturing workplace can also have an adverse effect on workers.
The most common health and safety hazards in the food manufacturing industry are:
If you are an employee who needs to report health and safety hazards in your food manufacturing workplace, you should follow your workplace’s procedures. This could include informing your line manager, supervisor or the most senior member of staff present at the time.
You may also be asked to submit a written report or provide photos or more information about the hazard. You should also inform other members of staff immediately so that the hazard doesn’t cause injury or illness before it is dealt with.
If you are a consumer or member of the public and you need to report a health and safety hazard, you should contact your local authority or the Food Standards Agency.
How to identify health and safety hazards
Identifying hazards is essential for risk management and ensuring the health and safety of all employees and the general public.
Both employers and employees should remain vigilant of hazards at all times and identify and eliminate them as quickly as possible.
Some ways you can identify health and safety hazards are:
How can health and safety managers ensure hazards are under control?
Once hazards have been identified and evaluated, it is the responsibility of health and safety managers to ensure that hazards are under control.
The most efficient way to eliminate or reduce hazards is by conducting a risk assessment. Risk assessments are a legal requirement for any employer who has more than five employees. A risk assessment should identify any potential hazards, what risks are involved in the activity and how these risks can be reduced or removed.
A risk assessment has specific steps that should be followed:
1. Identify hazards and any risk factors that could potentially cause harm.
2. Analyse and evaluate any risks associated with the hazard.
3. Determine the likelihood of harm and the severity of the potential harm.
4. Determine who is likely to be harmed and if any individuals are more at risk than others.
5. Determine appropriate and effective ways to eliminate, reduce or control risks.
6. Record all details of the risk assessment and update when necessary.
7. Ensure every relevant person reads and signs the risk assessment.
Why is it important to assess health and safety hazards?
Assessing hazards is not only a legal requirement, but it also helps to ensure the health and safety of everyone involved. Identifying hazards helps you to evaluate risks, and the effectiveness and suitability of any existing hazard controls and risk management measures.
Identifying hazards can also help you to implement any additional controls, utilise equipment or tools to reduce risks and remove hazards where possible.
Identifying hazards can considerably reduce the likelihood of work-related accidents, injuries and illnesses.
Assessing and eliminating hazards can also reduce work-related fatalities. In 2020/2021, 142 workers suffered fatal injuries at work, with the main causes of death being:
Identifying and removing hazards associated with these processes and others can help to reduce work-related deaths in the UK.
Contact us if you require further information.
If you’re found to be in material breach of Health and Safety law, you will have to pay for the time it takes the inspector to identify the breach and subsequently advise what you need to do to put things right. This includes investigating the issues themselves and taking any enforcement actions.
There are several key areas we’ve discovered are becoming more popular for the HSE to focus on. So, in addition to making sure your risk assessments are in place and up to date, here are some of the most common ones, and the most important checks you can make to make sure that you’re covered should an inspector turn up at your door.
CoSHH and occupational hygiene
Have appropriate COSHH assessments been completed for substances in use in your business?
If you’re welding, do you know the makeup of the fume and required control measures?
If welding is undertaken, can the fume be controlled at source via the use of on-tool extraction? Is Local Exhaust Ventilation a suitable alternative?
If you use metalworking fluids, have you assessed the risks to workers of long term exposure and inhalation? Do you have bacterial testing measures in place with records kept?
Has appropriate training, instruction and supervision been given to employees about hazardous substances within the workplace (consider cutting fluid, wood dust and welding fume) themselves? Have you communicated the risk / CoSHH assessment findings?
Has air/exposure monitoring been undertaken and recorded to ascertain suitable controls are in place?
Is Respiratory Protective Equipment required, if so what type?
Is a minimum assigned protection factor required?
Has face-fit testing been completed? (using a Fit2Fit accredited tester)
Has a DSEAR assessment been undertaken if required?
Can the dangerous substances identified be substituted for a less hazardous alternative, the quantity reduced, or the work process changed to reduce the risk?
Are measures in place to reduce employees exposed to effects of dangerous substance?
Do drivers have required training and licensing to drive the vehicle?
Is an appropriate evacuation and emergency procedure in place?
Noise and vibration
Have noise risk assessments been undertaken for the workplace and hearing protection zones / control measures implemented?
Have Hand Arm Vibration (HAV) and Whole Body Vibration (WBV) assessments been undertaken for the workplace and control measures implemented?
Is health surveillance in place where required for: Hazardous Substances, Noise and Vibration?
Machine maintenance and guarding
Has the task been risk assessed and a safe system of work developed?
Are all respective guards or interlocks in place? Have you inspected these prior to use?
Has the operational manual been reviewed to consider requirements for maintenance?
Have the operators and engineers been appropriately trained in process and maintenance requirements?
Is there a lock-out, tag-out procedure in place?
Prior to starting the work has the machinery been purged of any stored energy or hazardous substances?
Workplace transport
Has an appropriate risk assessment been completed that considers transport?
Has this considered blind spots? Bends? Pedestrian interactions? Gradients?
Is the site large enough for activities required? Loading/unloading, reversing etc.
Are vehicle routes wide enough for the types of vehicle needed?
Do drivers have required training and licensing to drive the vehicle?
Has a one way or traffic management system been implemented? What are the pedestrian segregation controls?
Working at height
Is a suitable and sufficient Risk Assessment in place?
Has it been completed by a competent person with involvement of the employees undertaking the work?
Has it been communicated to relevant parties? (i.e. those completing the work and those who may be affected by hazards arising from the work.)
Is the work at height planned, organised and carried out by competent persons?
Are ladders being used? Are they the correct type? Have they been inspected before the task is carried out?
Has adverse weather been considered if working outside?
Is access equipment being used? If so, what is the maintenance schedule? Is it the right equipment? Has it had its LOLER examination?
Is a work-restraint system in place? Is it suitable to prevent employees from accessing the edge/an area where they could fall?
Contact us if you require further information.