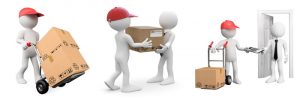
Health and Safety Hazards
According to statistics provided by the Health and Safety Executive (HSE), in the UK in 2020/2021:
DSEAR stands for Dangerous Substances and Explosive Atmospheres Regulations 2002, which requires employers to keep workers safe from the risks of fire, explosions and substances corrosive to metals.
DSEAR ensures that people are protected from these risks to their safety in the workplace, and to any members of the public that are in proximity of the working activities.
Both fire and health and safety assessments can be carried out to highlight where DSEAR regulations need to come into place, where the assessments find any issues involving dangerous substances and explosives that aren’t properly managed and controlled.
If a fire assessment was to flag a potential fire or explosion risk due to dangerous substances, DSEAR regulations can then be put in place to control and prevent an incident from taking place.
Fires and explosions create harmful physical effects, such as thermal radiation, oxygen depletion and overpressure effects. Substances that are corrosive to metal may cause damage to structures containing metal, which can reduce structural integrity.
Employers must:
Contact us if you require further information.
What is a DSE assessment
Most employers are required to carry out a DSE assessment, but what exactly is one, and what does it need to cover? To start, let’s understand what DSE is, then look at how we can assess it.
What is DSE?
DSE stands for Display Screen Equipment. As the name suggests, a DSE assessment is an assessment of Display Screen Equipment. Display Screen Equipment (DSE) is a device or equipment with a display screen and often refers to a computer screen. However, it includes both conventional display screens and those used in emerging technologies such as laptops, touchscreens and other similar devices.
In a work environment, desktop computers are traditionally looked at when considering DSE, but it is important to consider other display screens such as tablets, laptops and smartphones.
What is a DSE assessment?
A DSE assessment is an assessment of risk from the way we use computers, laptops, tablets and other display screens at work. Each workstation should be assessed, and the risks reduced as low as is practical.
A DSE assessment looks at how a user works at their workstation. Like any risk assessments, the aim is to identify the hazards and assess the likelihood and severity of harm to those that may be affected. Then, reduce the risk by altering the workstation or providing tools to make it comfortable.
If you have sat at a computer screen for a long time, you may already be familiar with some of the hazards. Poor posture or lack of movement throughout the day can lead to back pain. Staring at the screen for long lengths of time can give you headaches.
But it’s not just computer screens that are causing issues. Slouching over your phone, tablet or handheld device for even a short length of time can give you neck and upper back pain.
Why do we need a DSE assessment?
The Health and Safety (Display Screen Equipment) Regulations. These regulations lay out some key requirements for employers surrounding the use of DSE, one of which is the need to carry out a suitable and sufficient assessment of workstations used in the workplace.
2.—(1) Every employer shall perform a suitable and sufficient analysis of those workstations which – (regardless of who has provided them) are used for the purposes of his undertaking by users; or have been provided by him and are used for the purposes of his undertaking by operators The Health and Safety (Display Screen Equipment) Regulations 1992
Any workstation used by your business, regardless of who provides it, should be assessed. So DSE requirements apply to co-working spaces, remote working, temporary workplaces and your own offices.
However, this should not just be considered a tick box exercise to comply with legal requirements. A DSE assessment can actually help combat ill-health and conditions, such as epilepsy and therefore improve health and productivity in the workforce.
What does a DSE risk assessment cover?
Problems are often caused by the way we use our DSE. The display screen may not be the cause of back pain, but the way you sit at it could. Computer workstations or equipment can be associated with neck, shoulder, back or arm pain, as well as with fatigue and eyestrain.
So, it’s not just the display screen that needs to be assessed. Everything to do with the use of the equipment should be considered. Other items looked at in the assessment includes, the keyboard, the mouse, furniture and the environment.
The assessment should also encompass the general environment and includes lighting, reflections, glare, temperature, humidity and noise. All of these elements can impact how the equipment is used, and the risks to users.
The business benefits to DSE assessments
Display screen equipment are the most common tool used across all businesses, and can offer many benefits to a business including:
Improved health, wellbeing and morale for DSE users
Sustained production from reduced sick leave
Minimising the risk of compensation claims for upper limb disorders
Reduced administration costs
Encourages positive behaviour and adoption of DSE good practice.
Improved organisation safety
Contact us should you require a DSE Assessment.
The Walker Health and Safety blog is brought to you by the team at Walker Health and Safety Services Limited. You can contact us using the address or email address below or via the form on our main site.
e-Innovation Centre
University of Wolverhampton
Telford Campus
Priorslee
Telford
Shropshire
West Midlands
TF2 9FT
E-mail: info@walkersafety.co.uk
Telephone: 0845 834 0400
Fax: 0845 834 0401
Guest Blogging
If you feel that you could contribute to this blog then please feel free to send me a proposal of your guest blogging ideas and we can discuss these further info@walkersafety.co.uk . Please note any proposals must be of benefit to my readers from individuals with knowledge of their subject matter.
Many jobs now require the prolonged use of display screen equipment and legislation places specific duties on employers regarding its use. Take a look at our thoroughly revised and updated topic to make sure you are aware of what needs to be done.
Display screen equipment (DSE) is covered by the Health and Safety (Display Screen Equipment) Regulations 1992 (as amended), which promote the safe and effective use of DSE.
All aspects of the equipment and workstation are considered part of work with DSE.
The way in which DSE is used may lead to upper limb disorders, fatigue, stress or eye discomfort.
Excessive force, repetitive activities and poor postures are the three components perceived to be the biggest contributors to ill health associated with DSE work.
Appropriate set up of all features of the workstation can prevent discomfort from work with DSE. Contact us if you require a workstation assessment.
Selection of peripheral items for use with DSE can greatly improve the user’s comfort and effectiveness. Items must be selected for the person or the task to ensure suitability.
Rest breaks and changes of activity are essential in ensuring safe and effective work with DSE.
Checklists can be used to assess DSE work and ensure the workstation is suitable for the user to complete the required tasks.
Contact Walker Health & Safety Services for your health and safety requirements.
Health and Safety Hazards
According to statistics provided by the Health and Safety Executive (HSE), in the UK in 2020/2021:
What is a health and safety hazard?
A hazard is something that has the potential to cause harm or damage or have an adverse effect on a person or people. Many people confuse the words hazard and risk, especially in relation to occupational health and safety. The risk or level of risk is the likelihood that a person may be harmed or experience an adverse effect if they are exposed to a hazard. In other words, it is the likelihood that a hazard will have a negative impact on an individual’s health and safety.
Health and safety hazards can come from a variety of sources. Hazards can be substances, materials, processes and practices that can cause harm.
The most common health and safety hazards are:
Biological hazards
Biological hazards, often referred to as biohazards, can be any biological or organic substances that have the potential to cause harm or pose a threat to a person’s health. You may be exposed to biological hazards if you work with animals, people or infected plants. Biological hazards can have adverse health effects and in extreme circumstances can result in death.
Biological hazards can be found in a variety of workplaces, including hospitals, laboratories, schools, care homes, farms, and within the food industry.
An individual can be exposed to a biological hazard by having contact with any of the following:
Biological hazards are classified into four groups, depending on the level of risk of infection to humans, with Group 1 having the lowest risk and Group 4 having the highest risk.
Biological hazards can be transmitted in several ways, including by injection, absorption, ingestion or inhalation.
Chemical hazards
Chemical hazards are hazardous chemicals that can be in the form of a solid, liquid or gas. Some chemicals are more hazardous than others and they can result in a huge variety of health and physical effects, including skin irritation, breathing problems, respiratory system irritation and blindness.
Chemical hazards can be found in a variety of everyday products, meaning that many homes and workplaces involve a risk of coming into contact with chemical hazards, including hair salons, florists, restaurants, bars, schools and cleaning companies.
Chemical hazards may be present in the following products:
Hazardous chemicals are categorised according to how dangerous they are. Some of the categories include Harmful, Toxic, Very Toxic, Corrosive, Flammable, Extremely Flammable, Oxidising Agent, and Explosive.
Physical hazards
Physical hazards cannot always be seen or touched. They can be any factor or condition of the environment that can harm a person, even if they do not touch them.
People in a variety of environments can be exposed to physical hazards, including construction, demolition and excavation, as well as those who spend long periods outside.
Some examples of physical hazards include:
Ergonomic hazards are a result of physical factors such as body positions, the type of work you are undertaking, and any working conditions that can put a strain on your body. Many ergonomic hazards occur over time and can result in musculoskeletal injuries. Ergonomic hazards are often related to manual handling and can be found in all types of workplaces.
Musculoskeletal injuries can have significant short-term and long-term impacts on a person’s health and wellbeing.
They affect the musculoskeletal system which includes the muscles, tendons, bones, joints, ligaments, nerves and blood vessels. Common musculoskeletal injuries include back injuries, upper limb or neck disorders, lower limb disorders, and damage to joints or other tissue.
Ergonomic hazards include:
Safety hazards are hazards that create unsafe working conditions. Unsafe working conditions can cause injury, illness or even death. Safety hazards can be found in homes and workplaces across the UK.
Safety hazards can cause a significant number of injuries or illnesses and can even result in death.
Some examples of safety hazards include:
Environmental hazards are substances, states or events that can cause harm to people or have an adverse effect on their health. They are usually related to the weather, temperature and climate. They may be unpredictable or frequently changing, which is one of the reasons why they are considered hazardous.
Some examples of environmental hazards include:
Also known as work organisational hazards, these are hazards that can affect an employee’s mental health and wellbeing. An employee can experience both short-term and long-term effects of psychosocial hazards.
Some examples of psychosocial hazards include:
In 2021, the Health and Safety Executive (HSE) reported that there were 74,000 work-related injuries and illnesses in the constructions industry alone. Nearly 40,000 of these injuries were musculoskeletal disorders. Individuals who work in the construction industry are 2-3 times more likely to experience a workplace injury compared to other industries.
The main reason for the higher incidence of injuries in the construction industry is the high number of health and safety hazards.
Some of the most common health and safety hazards in the construction industry are:
Under the Health and Safety at Work etc Act 1974, employers are required by law to conduct a risk assessment of health and safety hazards on construction sites. This can help to reduce the number of hazards you are exposed to on a construction site.
However, self-employed and employed construction workers are not required to conduct a risk assessment if less than five people are working for them. This could mean that hazards and risks are not always reduced to the lowest possible level.
If you become aware of any hazards on a construction site you are working on, it is important that your report these hazards to the relevant people. This could be your employer, supervisor, a health and safety manager, or the site manager.
If you believe these concerns have not been taken seriously, or the hazard has not been dealt with, you could contact the Human Resources department of your company.
Alternatively, you can contact the Health and Safety Executive (HSE) directly. HSE is responsible for enforcing health and safety in many industries and workplaces across the UK.
There are many different members of staff working in different capacities and departments within a hospital. This includes doctors, nurses, other healthcare professionals, cleaning staff and administrative staff.
Health and safety hazards in hospitals can also differ depending on the area of the hospital you work in and the role you fulfil. Health and safety hazards can also affect patients and visitors to the hospital.
Being aware of potential hazards and removing or reducing them to the lowest possible level is therefore essential.
Some of the most common health and safety hazards in hospitals include:
All hospitals in the UK should have current risk assessments for many of the tasks, activities and operations that take place. However, if you believe the risk assessment is not accurate, or you have identified other hazards or risks, there are several procedures you can follow.
If you are a member of hospital staff and you need to report a health and safety hazard, the first person you should speak to is your line manager. Alternatively, you can consult another manager within the hospital or speak to the Human Resources department.
Many hospitals and healthcare settings will also have a formal system in place where you can submit a written report of your concerns.
If the issue concerns patient safety, NHS staff and the general public are encouraged to report the issue on the National Reporting and Learning System (NRLS). This helps the NHS to identify hazards and risks and improve patient safety.
Health and safety hazards in offices
Many people in the UK work in an office. You may think that an office is less hazardous than other workplaces, and although you are statistically less likely to incur an injury in an office compared to on a construction site, health and safety hazards in the office still exist and should be taken seriously.
Some of the most common health and safety hazards in an office are:
If you need to report a health and safety issue or the presence of hazards in your office, you should speak to your line manager or the office manager. Alternatively, you can contact your office or company’s Human Resources department or your union representative.
If you feel that your office is not taking your concerns seriously, or that the issue you need to report is especially serious, you can contact the Health and Safety Executive (HSE) and make a report on their website or via phone.
Health and safety hazards in warehouses
Ensuring the health and safety of warehouse staff can be difficult due to the many different tasks, activities and operations that are performed in a warehouse.
This can include handling heavy loads, operating machinery and equipment, packaging goods, assembly, production, loading and unloading goods, preparation of orders, and shipping.
Many health and safety hazards can be found in warehouses and if these hazards are not eliminated or reduced to the lowest possible level, employers are risking the health and safety of their employees.
Some of the most common warehouse health and safety hazards are:
Any warehouse employee who becomes aware of a hazard should report it as soon as possible. Your warehouse should have a procedure for reporting hazards and other health and safety concerns, and you should follow this procedure to ensure that the appropriate manager or supervisor can deal with the hazard as quickly as possible.
Health and safety hazards in food manufacturing
Food safety hazards can cause foodborne illnesses, injuries and allergic reactions. Hazards can affect food throughout the entire food processing, including during manufacturing.
As well as the health and safety hazards that can cause illness or injury to consumers, hazards within the food manufacturing workplace can also have an adverse effect on workers.
The most common health and safety hazards in the food manufacturing industry are:
If you are an employee who needs to report health and safety hazards in your food manufacturing workplace, you should follow your workplace’s procedures. This could include informing your line manager, supervisor or the most senior member of staff present at the time.
You may also be asked to submit a written report or provide photos or more information about the hazard. You should also inform other members of staff immediately so that the hazard doesn’t cause injury or illness before it is dealt with.
If you are a consumer or member of the public and you need to report a health and safety hazard, you should contact your local authority or the Food Standards Agency.
How to identify health and safety hazards
Identifying hazards is essential for risk management and ensuring the health and safety of all employees and the general public.
Both employers and employees should remain vigilant of hazards at all times and identify and eliminate them as quickly as possible.
Some ways you can identify health and safety hazards are:
How can health and safety managers ensure hazards are under control?
Once hazards have been identified and evaluated, it is the responsibility of health and safety managers to ensure that hazards are under control.
The most efficient way to eliminate or reduce hazards is by conducting a risk assessment. Risk assessments are a legal requirement for any employer who has more than five employees. A risk assessment should identify any potential hazards, what risks are involved in the activity and how these risks can be reduced or removed.
A risk assessment has specific steps that should be followed:
1. Identify hazards and any risk factors that could potentially cause harm.
2. Analyse and evaluate any risks associated with the hazard.
3. Determine the likelihood of harm and the severity of the potential harm.
4. Determine who is likely to be harmed and if any individuals are more at risk than others.
5. Determine appropriate and effective ways to eliminate, reduce or control risks.
6. Record all details of the risk assessment and update when necessary.
7. Ensure every relevant person reads and signs the risk assessment.
Why is it important to assess health and safety hazards?
Assessing hazards is not only a legal requirement, but it also helps to ensure the health and safety of everyone involved. Identifying hazards helps you to evaluate risks, and the effectiveness and suitability of any existing hazard controls and risk management measures.
Identifying hazards can also help you to implement any additional controls, utilise equipment or tools to reduce risks and remove hazards where possible.
Identifying hazards can considerably reduce the likelihood of work-related accidents, injuries and illnesses.
Assessing and eliminating hazards can also reduce work-related fatalities. In 2020/2021, 142 workers suffered fatal injuries at work, with the main causes of death being:
Identifying and removing hazards associated with these processes and others can help to reduce work-related deaths in the UK.
Contact us if you require further information.
A DSE assessment is an assessment of risk from the way we use computers, laptops, tablets and other display screens at work. Each workstation should be assessed, and the risks reduced as low as is practical.
A DSE assessment looks at how a user works at their workstation. Like any risk assessments, the aim is to identify the hazards and assess the likelihood and severity of harm to those that may be affected. Then, reduce the risk by altering the workstation or providing tools to make it comfortable.
The Health and Safety (Display Screen Equipment) Regulations. These regulations lay out some key requirements for employers surrounding the use of DSE, one of which is the need to carry out a suitable and sufficient assessment of workstations used in the workplace.
2.—(1) Every employer shall perform a suitable and sufficient analysis of those workstations which – (regardless of who has provided them) are used for the purposes of his undertaking by users; or have been provided by him and are used for the purposes of his undertaking by operators The Health and Safety (Display Screen Equipment) Regulations 1992
Any workstation used by your business, regardless of who provides it, should be assessed. So DSE requirements apply to co-working spaces, remote working, temporary workplaces and your own offices.
Display Screen Equipment.
We have put together an infographic. I would recommend that you share the information with employees as it could be beneficial to them.
Contact us for further information.
Guest Blogging
If you feel that you could contribute to this blog then please feel free to send me a proposal of your guest blogging ideas and we can discuss these further info@walkersafety.co.uk . Please note any proposals must be of benefit to my readers from individuals with knowledge of their subject matter.