Walker Health and Safety Services are assisting with the health and safety for this event and we are sponsoring an activity.
If you are interested in supporting them by sponsoring the event it would be great. Any money raised is going back into the community to enable them to have activities and events for the kids and to improve the community.
The have held a Christmas fayre, monthly walks and meetings for mums and babies.
or why not come along and support the local event.
Since the flyer was created, they have added a entry payment. Entry is £1 each and children have a range of activities to enjoy.
If you would like further information on the event, or would like to donated a raffle prize, let me know and I can pass on the information.
thanks
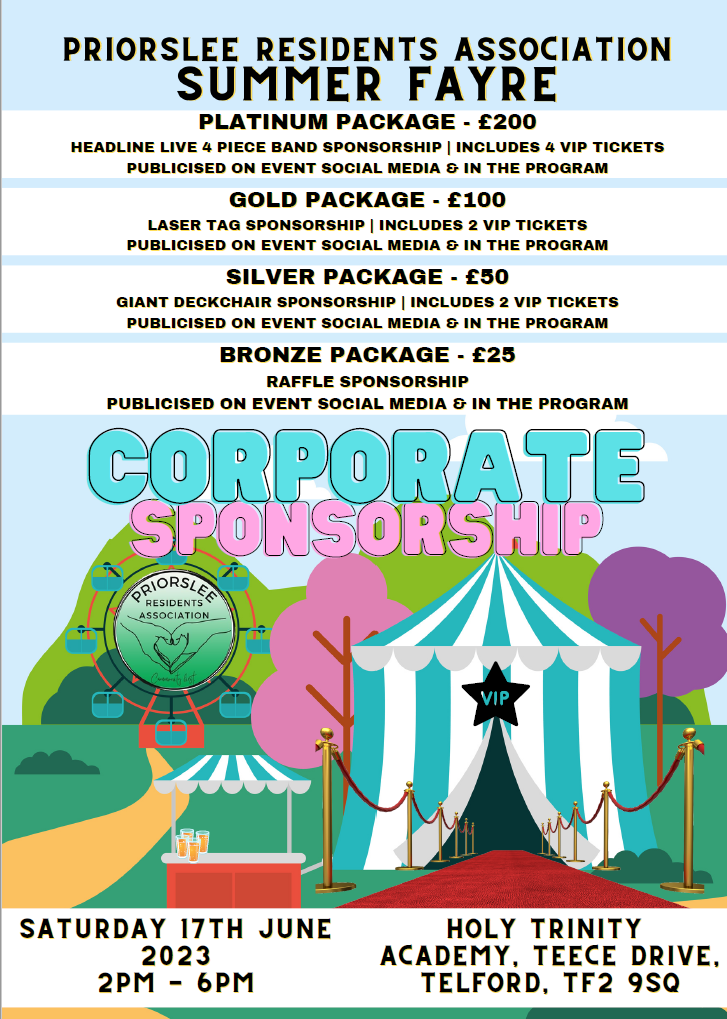

Contact us for further information by clicking here
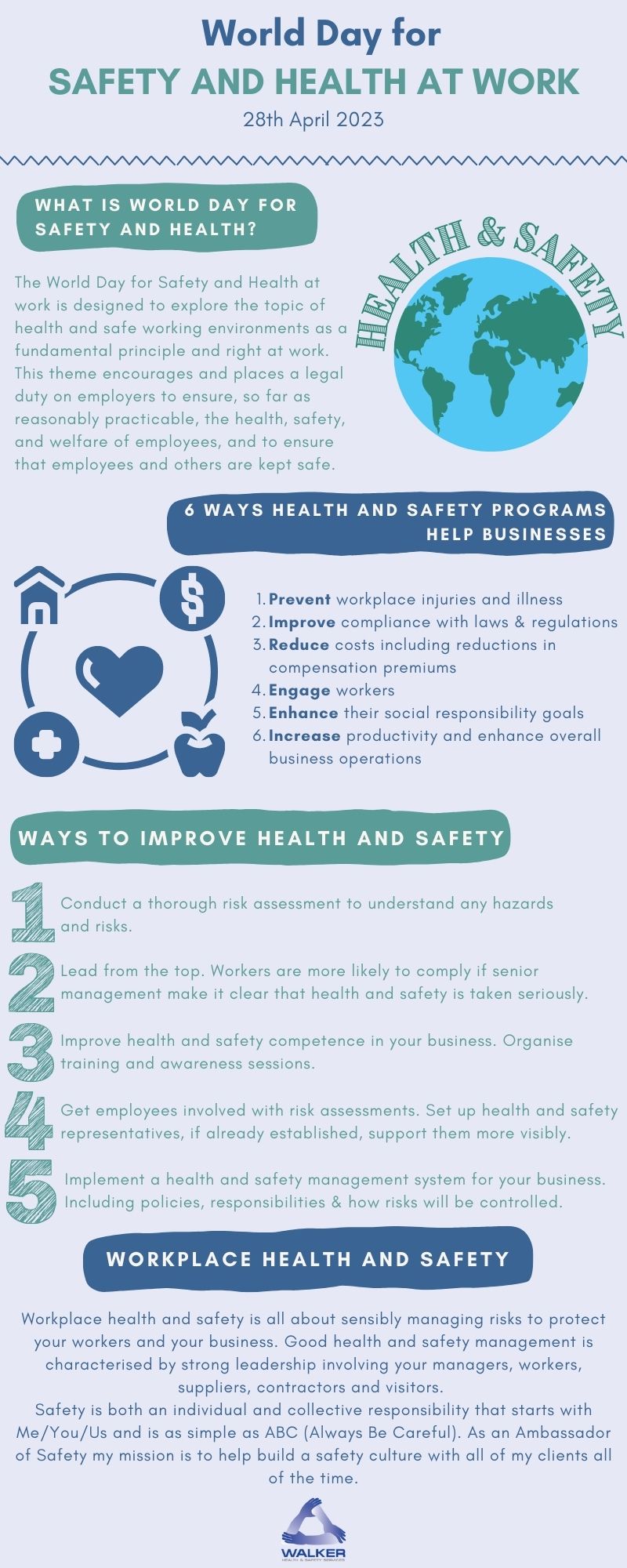
Here are three simple steps you can use anytime and anywhere to give yourself a boost and build your compassion for others.
By tuning in to your feelings, looking for what’s good and sharing kindness you can nurture yourself and help make things better day by day.
Please give it a try and, if you find it helpful, share it with others too.
Follow these useful links for further information.
#Contact us.
#WalkerHealthandSafety
#Training
#Wellbeing
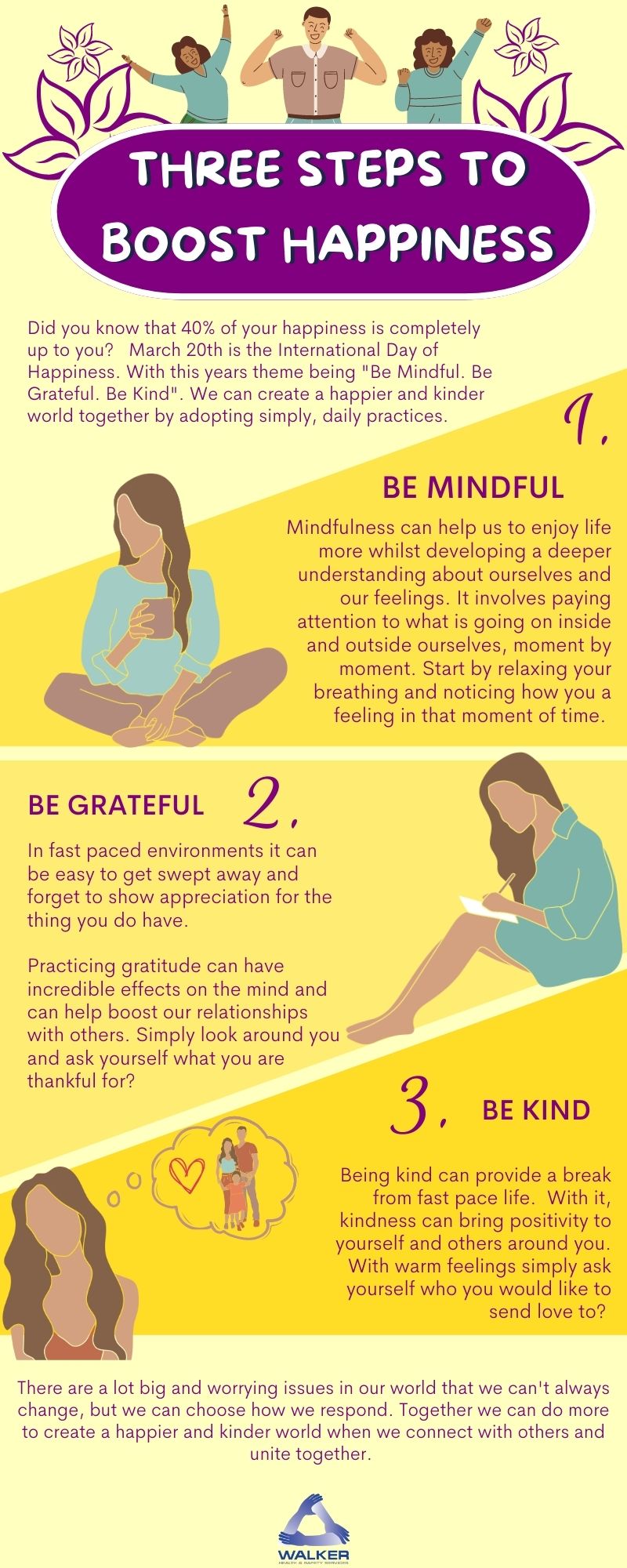
Presentations from the Health and Work Conference 2022
PowerPoint Presentation (bhsea.org.uk)