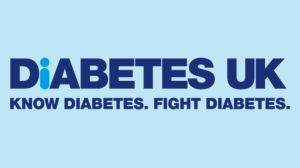
What is diabetes?
Diabetes is a chronic condition where the body is unable to regulate its glucose levels as a result of either the pancreas failing to produce insulin, or insufficient insulin to help glucose enter the body’s cells. Alternatively, the insulin that is produced does not work properly (known as insulin resistance (IR)). These are the two main types of diabetes:
- type 1 is a less common condition, usually developing in children and young adults; with this type of diabetes, the body is unable to produce insulin to manage glucose levels in the blood
- type 2 is far more common and mainly appears in adulthood; in this type of diabetes, the body does not produce enough insulin or the body’s cells do not react to insulin.
Genetics certainly increase the chances of getting both types of diabetes, but it is accepted that certain factors, particularly overeating and a sedentary lifestyle increase the risk of type 2 diabetes. Other factors include age, being overweight or obese, body fat distribution, family history and ethnicity.
Diabetes can lead to heart disease, stroke, kidney disease, vision problems and lower limb amputation if it is not properly controlled.
Diabetes and safety in the workplace
While it is a serious condition, diabetes is a very common lifelong health condition that does not hinder people’s ability to get a job or to keep one. The law requires that people with diabetes be assessed on their individual ability to do a job and not to be discriminated against simply because they have the condition.
However, some safety critical jobs will have legitimate health requirements that may exclude people with certain medical conditions. There are some key areas of employment, such as driving long goods vehicles or those carrying passengers, where there are restrictions on people with insulin-dependent diabetes.
Concerns about workplace safety in relation to diabetes tend to be associated with the development of hypoglycaemia — a state of low blood glucose. Symptoms of hypoglycaemia can include hunger and dizziness as well as confusion and unconsciousness. Hypoglycaemia is commonly perceived as a concern for people with type 1, rather than type 2 diabetes, although hypoglycaemia is a potential risk for anyone using insulin and many people with type 2 diabetes are insulin-dependent.
In contrast, hyperglycaemia occurs when blood glucose is high because the body has too little insulin or is improperly using insulin, resulting in symptoms such as hunger, thirst and frequent urination. Left untreated, hyperglycaemia can lead to diabetic coma. However, the symptoms of hyperglycaemia generally develop over hours or days and do not occur suddenly. Therefore, hyperglycaemia does not pose an immediate risk of sudden incapacitation.
Diabetes awareness at work
It is estimated that around half a million people in the UK have diabetes but are unaware that they have it. Given that many of us may also be at risk of developing type 2 diabetes in the future, Diabetes UK says that holding a diabetes awareness day could make a big difference to the health and wellbeing of staff (see Diabetes UK website for information in this regard).
Employers could of course also use their existing wellbeing programmes to raise awareness about the condition, including information about the value of keeping active, eating healthily and maintaining a healthy weight.
Type 2 diabetes isn’t inevitable. Up to 80% of cases of type 2 diabetes can be delayed or prevented, so it’s important that everyone understands their risk, so they can reduce their chances of ever developing the condition.
Mental Health and Work
Contact us for further information.
With the recent heat waves, thermal comfort in the workplace is now becoming something of a challenge for many employers. Whilst there is no maximum workplace temperature specified in the UK, the Workplace (Health, Safety and Welfare) Regulations 1992 state that workplaces shall be maintained at a ‘reasonable’ temperature. What is ‘reasonable’ will depend upon the nature of the work, but according to the HSE, an acceptable level of thermal comfort lies somewhere between 13°C and 30°C.
Workers likely to be most at risk include catering staff, outdoor workers e.g. horticultural workers, maintenance personnel, process workers and employees who must wear personal protective equipment (PPE) such as breathing apparatus or impermeable clothing. Employees working in offices which do not have air conditioning are also likely to be affected by hot weather.
It is important to continue wearing PPE during extreme temperatures. However, encourage staff to remove them during break times to cool off, sit in the shade or a cool area and drink plenty of fluids, this will help to reduce heat stress. Heat stress is where the body is under stress from over heating. Heat related illnesses include heat cramps or heat stroke, each with its own symptoms and treatments. Symptoms can range from profuse sweating, heat rash, fainting, loss of concentration.
10 Top Tips for Dealing with the Heat
- Consult with your employees to establish reasonable levels of thermal comfort for the majority, but accept that you won’t be able to please everybody.
- Carry out a risk assessment and identify employees who are most susceptible to heat stress, e.g. pregnant women. Consider altering work patterns to reduce the level of risk by job rotation, working at cooler times of the day. Limit exposure of outdoor workers by providing sunscreen and suitable clothing, e.g. long sleeves and hats.
- Modify the working environment by providing mobile air conditioning units, but not oscillating fans, as these simply circulate warm air. Use window blinds or shades to help reduce the effects of heat and solar gain.
- Provide more frequent breaks in a cooler environment – the hotter the working environment and more strenuous the work, the more frequent breaks should be.
- Ensure a constant supply of drinking water and stress to staff how important it is to maintain hydration at work. Caffeine-based drinks can actually speed up dehydration, as they are diuretic. Coffee also speeds up metabolism, thereby increasing body temperature.
- If you have a dress code, consider relaxing it, as it’s better to have productive, casually-dressed employees, than employees who must leave work because they feel unwell.
- Ask staff to turn off electrical equipment when leaving the office. Power used to keep items on stand-by is dissipated into the workplace as heat.
- Do big print runs and other heat generating jobs in the cooler part of the day.
- If office temperatures are unbearable for some, consider allowing them to work from home.
- Review PPE provision to see if there is any which is cooler and more comfortable and which can offer the same (or better) level of protection.
Your risk assessment must take into account factors such as temperature to protect your employees, as well as helping you stay on the right side of the law.
If you require advice please contact us.
As the warm weather continues, the dangers of working outside also increases. Knowing how to work safely in hot weather can help prevent heat stress and heat stroke. Heat stroke is the most serious heat-related disorder and occurs when the body can no longer control its temperature. The body temperature can rise to 106 degrees Fahrenheit or higher within 10 to 15 minutes and heat stroke can cause death or permanent disability if emergency treatment is not provided. Other heat-related disorders include heat exhaustion, heat cramps and heat rash.
Heat stroke occurs when the body no longer sweats and body temperature reaches dangerous levels. Symptoms of heat stroke include:
- Dry, hot reddish skin and lack of sweating
- High body temperature
- Strong, rapid pulse
- Chills
- Confusion
- Slurred speech
Heat exhaustion is the body’s response to the loss of water and salt, typically through sweating. Symptoms of heat exhaustion include:
- Excessive sweating
- Weakness or fatigue
- Dizziness and/or confusion
- Clammy skin
- Muscle cramps
- Flushed complexion
Heat cramps are painful cramps in the body’s muscles due to low salt levels and are typically caused by excessive sweating. Symptoms of heat cramps include:
- Muscle pain usually in the abdomen, arm or legs.
- Muscle spasms usually in the abdomen, arm or legs.
Heat Rash is an irritation of the skin caused by excessive sweating. Symptoms of heat rash include:
- Red cluster of pimples or small blisters
- Usually on neck and upper chest, groin area, under the breasts, and in elbow creases.
Ten Hot Weather Safety Tips:
- Stay hydrated. Drink plenty of fluids.
- Avoid dehydrating liquids. Alcohol, coffee, tea and caffeinated soft drinks can hurt more than help.
- Wear protective clothing. Lightweight, light-colored and loose-fitting clothing helps protect against heat. Change clothing if it gets completely saturated.
- Pace yourself. Slow down and work at an even pace. Know your own limits and ability to work safely in heat.
- Schedule frequent breaks. Take time for rest periods and water breaks in a shaded or air conditioned area.
- Use a damp rag. Wipe your face or put it around your neck.
- Avoid getting sunburn. Use sunscreen and wear a hat if working outside.
- Be alert to signs of heat-related illness. Know what to look for and check on other workers that might be at high risk.
- Avoid direct sun. Find shade or block out the sun if possible.
- Eat smaller meals. Eat fruits high in fibre and natural juice. Avoid high protein foods.
Stay safe this summer, keep hydrated.
In June 2017 we had a weather warning heat health watch. Read here for further details.
Contact us should you require further information.
The Health and Safety at Work Act, etc 1974 states that employers should provide “such information, instruction, training and supervision as is necessary to ensure, so far as is reasonably practicable, the health and safety at work of his employees”. The Management of Health and Safety at Work Regulations 1999 further require that employers provide employees with adequate health and safety training both on recruitment and when the risks to which they are exposed change, for example, where they move to a new role or when new work equipment is provided.
The Management of Health and Safety at Work Regulations 1999 go on to state that training should be repeated periodically where appropriate, be adapted to take account of any new or different risks and take place during working hours. Other sets of regulations which require training of employees include the Health and Safety (Display Screen Equipment) Regulations 1992, the Health and Safety (First-Aid) Regulations 1981, the Provision and Use of Work Equipment Regulations 1998 and the Regulatory Reform (Fire Safety) Order 2005.
Organisations that have their health and safety management systems certified, for example to BS OHSAS 18001 or ISO 45001, are also required to conform to requirements concerning competence.
Unfortunately, when it comes to work-related training, there is no one-size-fits-all. Employers should consider who in their organisation needs training, what training should be provided, when, by whom, and when training should be repeated and refreshed. Consideration should also be paid to whether staff require formal qualifications for their role, such as facility managers, first aiders, or the maintenance teams responsible for legionella safety.
Ensure Employees follow Your Training: 5 Top Tips. Click here
Training – Contact Us for your training requirements or to discuss training solutions. Click here to look at our website training page.